
- #FRC DRIVER STATION AXIS M1013 SERIAL#
- #FRC DRIVER STATION AXIS M1013 DRIVERS#
- #FRC DRIVER STATION AXIS M1013 FULL#
It connects to sensors, Jaguar and Victor motor controllers, and Spike relays via PWM cables. The Digital Sidecar connects to a cRIO module with a DB37 ribbon cable. The signals it sends are used for controlling devices such as motor controllers or servo motors. The signals it receives are sent from sensors that output digital signals, such as an encoder or the pneumatic pressure switch. The Digital Sidecar is a module that acts as a hub for the digital signals that are sent to and from the cRIO.
#FRC DRIVER STATION AXIS M1013 SERIAL#
Finally, the cRIO has a serial port which can be used to connect with the Jaguars through a CAN bus, which is one option for controlling the Jaguars.
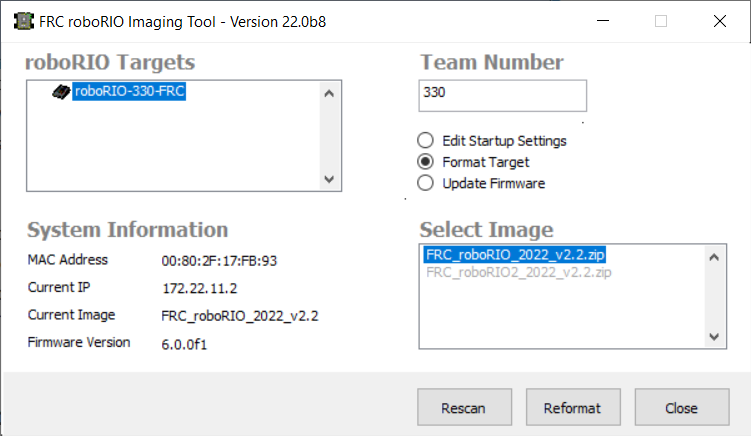
It connects to the D-Link Router with an Ethernet cable allowing it to communicate with other components connected to the Router, as well as wirelessly with the Drive Station. The cRIO is powered by a 24V connection from the Power Distribution Board. Its swappable modules can be used to connect it to the Digital Sidecar, the Analog Breakout, and the Solenoid Breakout. The cRIO-FRC II was given to rookie teams starting in 2012, with veteran teams having the option to purchase one.Īs the metaphorical brain of the robot, the cRIO connects with many different parts of the control system. This smaller number of supported modules also translates to a lighter cRIO with a smaller footprint. The cRIO-FRC supports eight modules, while the cRIO-FRC II supports four. The only practical difference between these two versions is the number of modules they support. The cRIO-FRC is shown in the first picture and the cRIO-FRC II is shown in the second. There are two versions of the cRIO that teams may encounter.
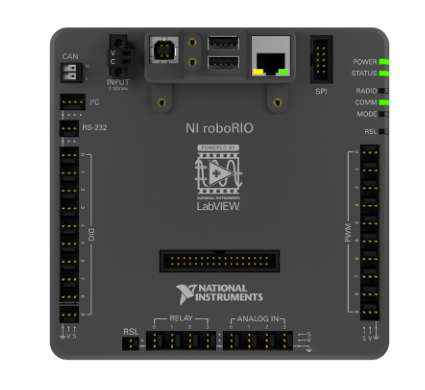
The cRIO is modular, allowing teams to customize it to suit the needs of their robot. While its operation can be as simple as mapping joystick values to motor speeds, it can also execute complex control loops and automated commands.
#FRC DRIVER STATION AXIS M1013 DRIVERS#
Using code generated in LabVIEW, C++, or Java, it takes inputs from the drivers and sensors and outputs instructions to motors, pneumatic solenoid valves, and other devices.
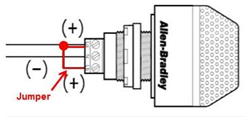
The cRIO is the central processing unit of a FRC robot.
#FRC DRIVER STATION AXIS M1013 FULL#
It uses a digital signal to communicate that the shaft it is attached to has rotated a certain amount – “1 count.” The number of counts per full revolution varies between encoders, but can be anywhere from one to one thousand per revolution. Several motor controllers are connected serially to the same network and then controlled from the central processor.Įncoder: An encoder is a sensor used to measure rotation. Most commonly, they have three wires, but there exist versions with anywhere from one to 5 cables.ĬAN: In FRC, a Controller Area Network (CAN) is used to control motor controllers. PWM Cable: A Pulse-Width Modulation (PWM) cable is a cable commonly used to allow robot components to communicate with each other, using either digital or analog signals.

Robot components that use analog signals communicate by varying the voltage of the signal. Robot components that communicate with a digital signal generally do so by varying the frequency at which they alternate between on and off.Īnalog Signal: Unlike a digital signal, which has discrete values, an analog signal’s output has a continuous range of values. Digital Signal: A digital signal has only two states: on or off.
